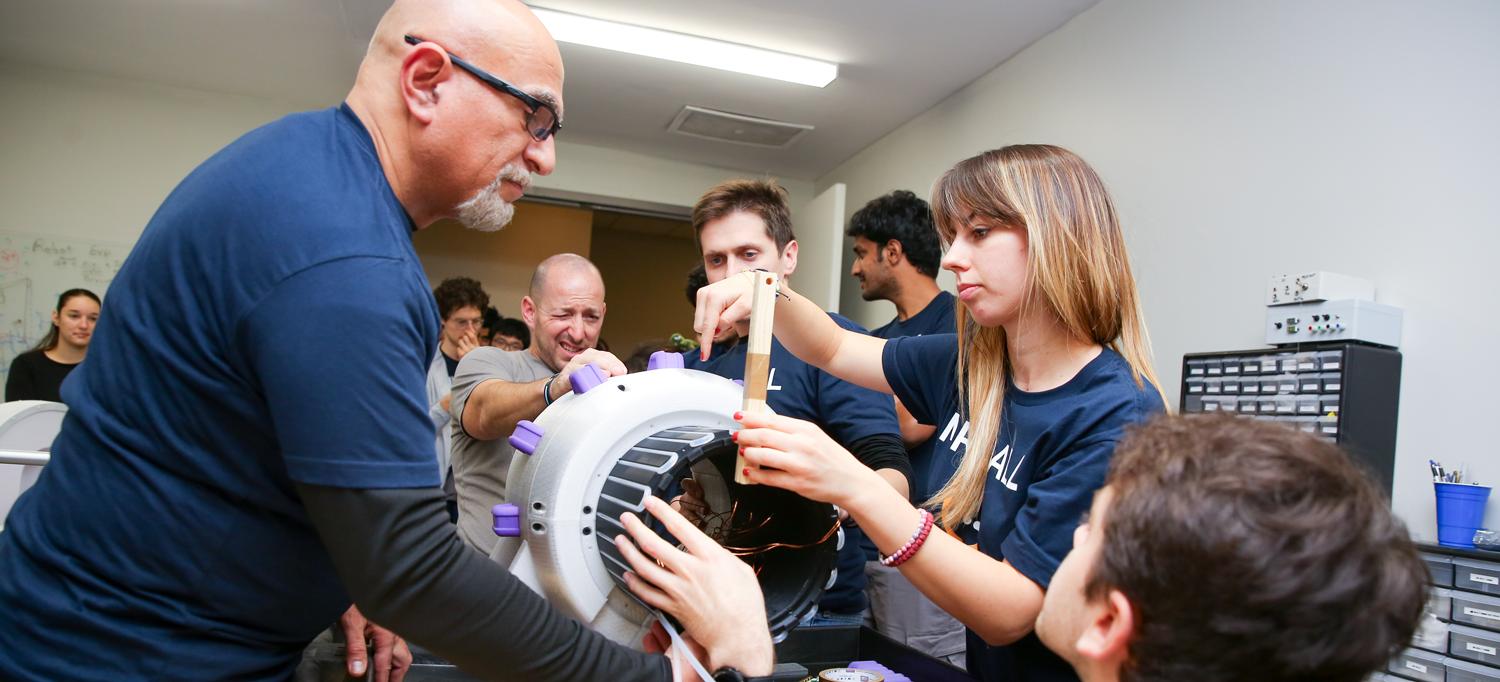
The Department of Radiology’s MRI4ALL Hackathon results prove that MRI scanners can be less costly to develop.
Photo: NYU Langone Staff
MRI scanners are costly and difficult to develop. But do they need to be? A team of researchers from the NYU Langone Radiology—Center for Biomedical Imaging convened over four days to build a functional MRI machine from scratch. The results laid the groundwork for a more equitable model of making medical imaging technology accessible to underserved areas around the globe.
A typical clinical MRI scanner weighs up to 17 tons and can cost as much as $3 million. Each machine requires three dedicated rooms—one for scanning, one for electronic attachments, and another to scan the patient. Its size, cost, and the expertise required to operate it put it out of reach for many healthcare providers in developing countries.
To make MRIs more affordable and accessible for healthcare providers in underserved areas around the globe, researchers at NYU Langone’s Department of Radiology—home to a team of 150 researchers and 41 research faculty—held its inaugural MRI4ALL Hackathon. The event, attended by 52 scientists from 16 institutions, including 21 scientists from NYU Langone, started on October 16, spanned four days, and took place across several Manhattan locations.
“The need for MRI technology in medicine is poised to keep growing,” says lead organizer Leeor Alon, PhD, assistant professor in the Department of Radiology at NYU Langone Grossman School of Medicine. “Because this equipment is so expensive and currently offered by only a few vendors, our goal was to create an open-source community that can build MRI scanners with greater ease. This was the first hackathon that covered the creation of a whole MRI machine, and it was the first to do it in just four days.”
Participants were divided into four teams: one focused on assembling the magnet—or, more precisely, the set of 990 magnets meticulously arranged to produce a stable field; one to build the “gradient coils,” loops of wire that allow for spatial encoding of the MR (magnetic resonance) signal; a group to assemble the radio frequency transmitter and receiver; and a team developing the software that controls these components and displays the images.
Researchers toiled into the wee hours to assemble their respective parts. “People didn’t want to stop,” says Dr. Alon. “They wanted to get this machine to work.”
On the final day of the event, the teams convened to unite their separate sections into an 80-pound machine, roughly 2 feet wide and with an opening large enough to fit a wrist or ankle. Kai Tobias Block, PhD, an associate professor of radiology who formerly worked for Siemens Healthineers, a leading manufacturer of MRI machines, says the process of integrating components into a novel system typically takes weeks. “We had just two to three hours,” Dr. Block says. “It was very challenging. Every component is highly attuned, and they need to work perfectly with each other.”
NYU Langone’s MRI4ALL Hackathon by the Numbers
- Days to completion: 4
- Total participants: 52
- Participants from NYU Langone: 21
- Total participating institutions: 16
- Magnets used (type N40UH): 990
- Pieces of code added to the software: 950
- Cost of components: $15,000
- Weight of MRI scanner: 80 pounds
- Bagels eaten: 208
To put their model to the test, the team used what is known as a “phantom,” a simple water-filled test object whose exact dimensions and contents were known only to one member of the team. If the machine produces an accurate image, it indicates that the scanner works properly. After a few false starts, the DIY machine yielded clear images. “Eventually, after resolving multiple technical issues, the scanner produced correct reconstructions of the phantom,” says Dr. Block. “That was the result we were hoping for.”
With this important proof of concept, the project participants hope to inspire others to build upon their open-source scanner, which the team named Zeugmatron Z1—a reference to the word “zeugmatography” that Nobel Prize recipient Paul Lauterbur originally proposed when he invented the MRI principle 50 years ago.
“This was the first hackathon that covered the creation of a whole MRI machine, and it was the first to do it in just four days.”
—Leeor Alon, PhD
The team is now making all the designs for the components, many of which were 3D printed, as well as the software developed and tools used for designing the magnet, publicly available on their project website.
“The hope is that our community will keep innovating and improving the technology,” says Dr. Alon.